|
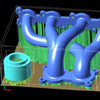 |
|
南加大华裔教授 Yong Chen 教授关于三维喷印(3D Printing)研究 |
|
2013/6/18 15:35:55 | 浏览:4470 | 评论:4 |
|
|
|
|
Prof. Yong Chen(YongChen@usc.edu)
Epstein Department of Industrial & Systems Engineering,
University of Southern California, Los Angeles, California
Manufacturing has been a big contributor to improved quality and sustainability of human life. The layer-based Direct Digital Manufacturing(DDM, or 3D Printing)is a new type of manufacturing process that can directly fabricate a physical object from a Computer-aided Design(CAD)model. It has been widely recognized as a disruptive manufacturing technology for a wide variety of applications such as aerospace, defense, biomedical and consumer products to name a few. In addition, DDM potentially enables revolutionary new designs by incorporating complex three-dimensional shapes, heterogeneous material properties and multi-functionality. Such potentials, if fully realized, would fundamentally change the design and fabrication of future engineering systems. |
Since the Direct Digital Manufacturing involves both physics-based manufacturing and computation-based design and control, the key of success in addressing DDM-related challenges is to be able to fuse theoretical, computational and experimental knowledge with systematic thinking. This interdisciplinary research philosophy by tightly integrating both hardware and software sides of DDM technology is also at the core of my research lab. My research covers four topical areas in recent years:(1)Novel process and machine development for direct digital manufacturing and personal 3D printing;(2)New modeling and control techniques for accurate and reliable direct digital manufacturing process;(3)New design methods for DDM-enabled products and applications; and(4)New modeling and computing methods for DDM-enabled complex geometries. A brief summary of them is given as follows.
R1. Novel process and machine development for direct digital manufacturing and personal 3D printing
| Manufacturing processes can be generally classified into additive-based, subtractive-based, and deformation-based processes. DDM is mainly based on the layer-based Additive Manufacturing(AM)processes. Various AM processes have been developed and commercialized over the past 25 years. However, even with the significant development, the AM processes are only a small portion of the manufacturing processes that have been developed by considering various requirements on shapes, materials, speed, cost, quantity, accuracy, flexibility, etc. Based on digital devices such as the Digital Micromirror Device(DMD)and inkjet print head, we developed a set of novel AM processes to enable multi-materials(refer to Figure 1), heterogeneous materials(refer to Figure 2), functional materials(refer to Figure 3), high speed(refer to Figure 4), etc. |

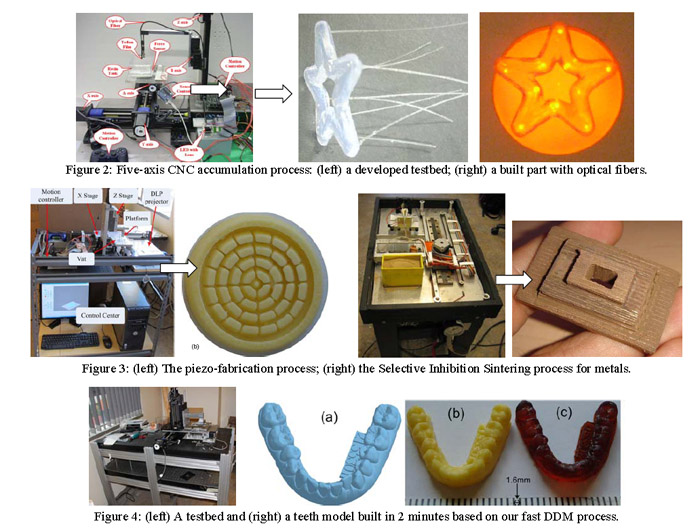
R2. New modeling and control techniques for accurate and reliable direct digital manufacturing process |
The layer-based additive manufacturing(AM)processes were originally developed for rapid prototyping(RP)during product development. Significant advances in material, process and machine developments have enabled AM processes to start to be used in direct product manufacturing. However, such direct manufacturing applications pose requirements such as much higher accuracy, better surface finish, higher degree of manufacturing automation, shorter building time, and capable of achieving predictable material properties, etc. To address such requirements, we have developed new modeling and control methods for the MIP-SL process on accuracy and resolution(refer to Figure 5), surface finish(refer to Figure 6),
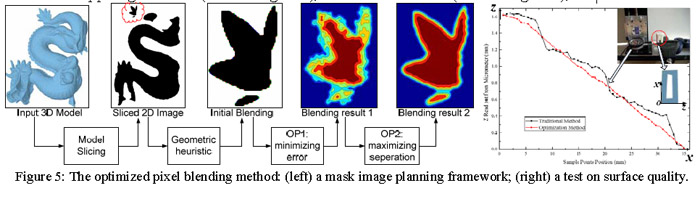
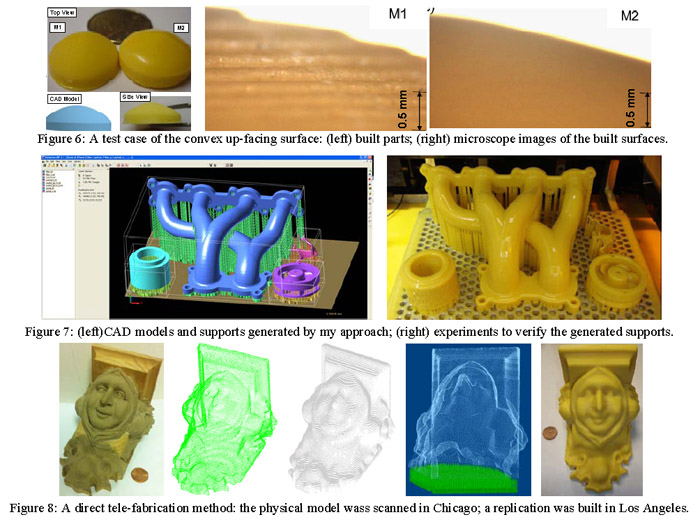
R3. New design methods for DDM-enabled products and applications |
The benefits of using DDM’s unique capabilities such as unlimited geometric capability and heterogeneous material property for better design performance are mainly untapped. Current computer-aided design(CAD)tools(e.g. Pro-Engineer and SolidWorks)are developed for traditional manufacturing processes, which pose severe limitations on the designed shapes and materials. To address several fundamental research issues in the Design for DDM(DfDDM)area, we have developed several design methods and related CAD tools including lightweight internal structure design(refer to Figure 9), flexible structures(refer to Figure 10), and customized surfaces(refer to Figure 11), etc. |
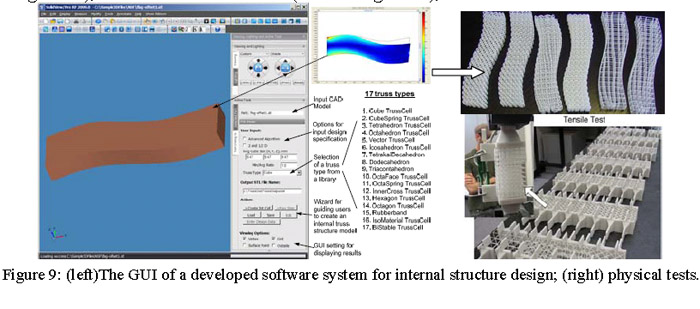
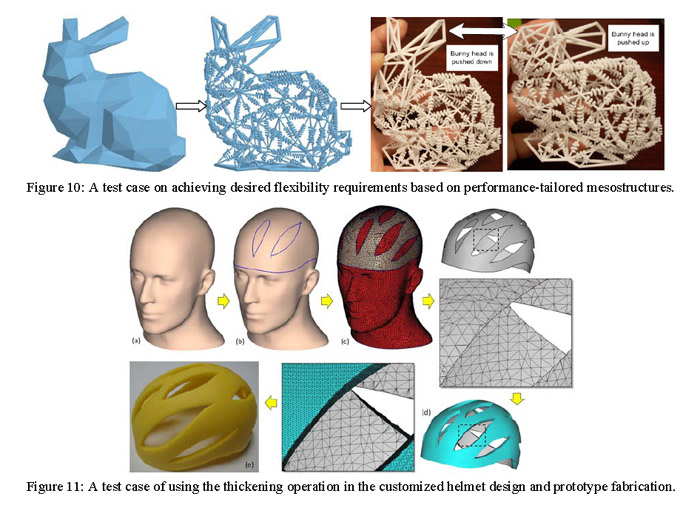
|
R4. New modeling and computing methods for DDM-enabled complex geometries |
Geometric modeling and computation are essential for computer-aided design and manufacturing. Direct digital manufacturing can cost-effectively fabricate complex three-dimensional(3D)shapes. However, to design and fabricate future product components whose shapes would be orders of magnitude more complex than those of current product design, new geometric modeling and computing methods are required that have superb robustness and efficiency for complex geometries. We develop a new type of geometric modeling and computation method based on a novel structured-point-based representation named Layer Depth Normal Images(LDNIs)and used them in various applications including offsetting(refer to Figure 12), Boolean(refer to Figure 13), and mesh regulation(refer to Figure 14). |
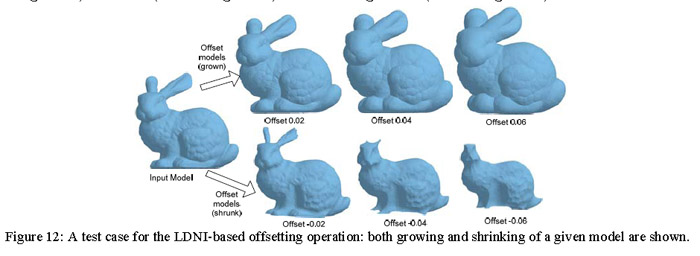
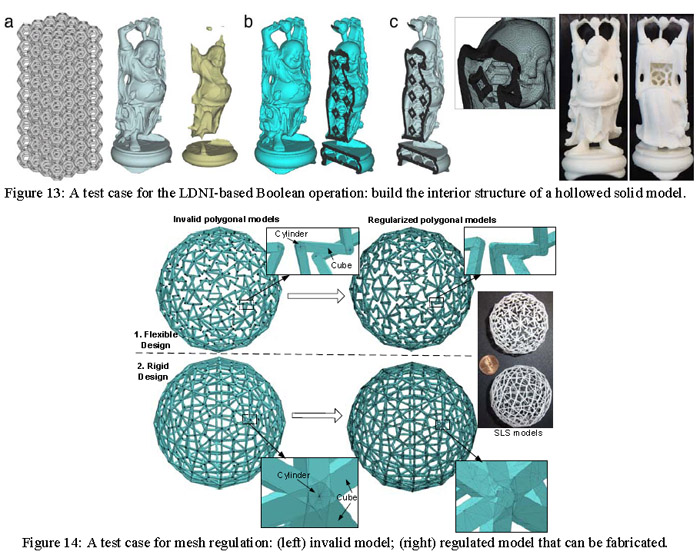
|
|
|
|